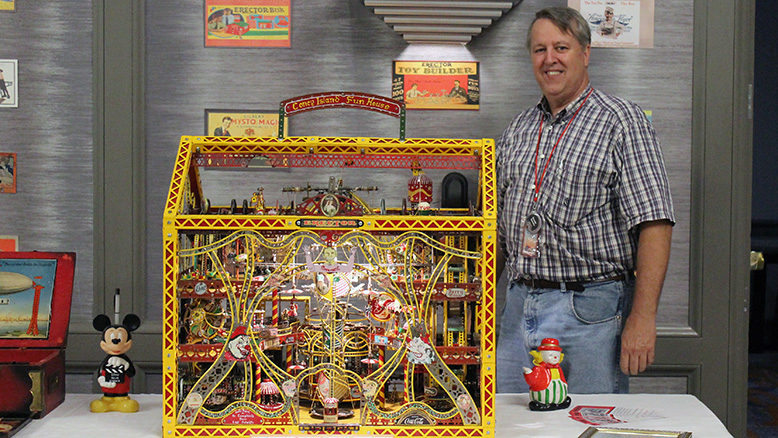
Randy Sauder’s Coney Island Fun House
Reprinted from the September 2013 ACGHS Newsletter Hello Boys & Girls. This original design to honor A. C. Gilbert’s 1913 founding was built over two years in about 1,000 man-hours. That’s roughly the same a working an 8-hour day, 40 Read More …